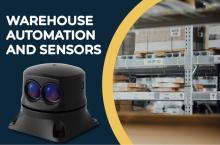
Warehouse Automation and Sensors
How can you automate your warehouses? Should you automate your manufacturing? This article is an extension of our Hokuyo and Yujin post, and goes into more depth about warehouse automation.
Why Automate Warehouses?
Let's address the elephant in the room. Are robots going to steal human jobs? No. In fact, many manufacturing and warehouse managers are "employing" robots to improve human employee retention.
Warehouse automation solutions can reduce the number and severity of workplace injuries and errors in addition to allowing humans to perform more complicated, strategic tasks. Beyond these improvements, autonomous mobile robots can dramatically increase productivity.
By utilizing automation in manufacturing, warehouse inventory, sorting, shipping, and receiving, many organizations are increasing their customer satisfaction and decreasing their downtime--in spite of supply chain delays.
How Robotics and Sensors Work in Automated Manufacturing
The use of robots is not new and the benefits are widespread. Robots require input to perform their programming. The input a robot receives from its environment--along with internal regulation--comes from sensors. A variety of sensors can be added to a given autonomous system for pressure detection, heat sensing, filling accuracy, and object avoidance (to name a few examples).
The benefits of using automation in manufacturing are similar to those for warehouse management. With robots performing many repetitive tasks, you get:
- Consistent and higher-quality parts
- Decreased down time
- Less limitations on production
- Improved productivity
- Decreased workforce injuries
- Improved employee retention, because your human workforce will be able to perform more meaningful tasks.
Exactly like the case of automated mobile robots, the sensors used for manufacturing robots are the key to success. It’s a win-win if your robots have the best possible sensors for their roles.
If you skimp on sensors, you may find yourself in the frustrating position of paying for frequent recalibration or replacement of sensors.
Warehouse Automation Solutions Can Improve Warehouse Management Systems
Beyond lowering cost, automation technologies can be extremely useful in enhancing efficiency, accuracy and productivity in day-to-day operations.
Challenges of Warehouse Management and Opportunities for Automation Solutions
Worker shortages, the Great Resignation, supply chain slowdowns, and COVID restrictions have overloaded a previously growing demand. This makes the job of warehouse and product manufacturing managers more difficult than ever.
We won't pretend to be experts in warehouse management. However, we are experts in automated and autonomous systems. Sensors and robotics used in automated mobile robots and automated guided vehicles can give warehouse managers and employees more peace of mind and safety in meeting these demands.
What processes can be automated?
How does mitigating lost inventory, better data analytics, and increased ROI sound? That's what physical and digital automation can offer most modern warehouses and manufacturing facilities.
Digital and Physical Automation
There are two categories of automation: physical and digital. Some examples of physical automation solutions include (but are not limited to) the following:
- Product picking and sorting
- Receiving and retrieval systems
- Shipping
- Item transport
- Manufacturing processes
- Material handling equipment
Digital automation is the use of software to automate data collection and other information systems. Think of anything that can be done with pencil and paper--there's likely a digitally-optimized way it can be done.
Many companies find it more simple to first incorporate digital automation (barcode scanners, for instance) as it has a lower starting cost and significant effect on efficiency and accuracy.
As available space decreases and complexity of processes and orders increase, physical automation solutions become necessary to maintain or develop company growth.
Source: https://www.netsuite.com/portal/resource/articles/inventory-management/warehouse-automation.shtml
Processes That Benefit From Physical Automation
It would take an inordinate amount of scrolling to cover each opportunity for physical automation with AMR's and AGV's. Instead, we'll focus on inventory management and how robotics and sensors can improve this crucial business component.
AMR's and Sensors for Inventory Management
AMR's, AGV's, and solo sensors have been used for inventory management for a while now. They've proven their benefit for decreasing mistakes, increasing efficiency, and improving time-to-delivery. Inventory management systems include accurate counting, receiving, storing, and transporting of product.
Automate Product Count with Sensors
LiDAR sensors, specifically, are used in many automated manufacturing and warehouse facilities. LiDAR sensors project and receive pulsed light to determine the distance from an object using time of flight (ToF) principles.
Imagine your warehouse stores and ships coffee filters that come in 1 ft by 1ft boxes. A LiDAR sensor placed above the stack of boxes can--with the help of microprocessor and appropriate WMS--tell you when you're low on coffee filter stock.
AMR's and AGV's Automate Product Transport and Sorting
Let's say you have another type of coffee gear in your warehouse, like fancy glass carafes.
The glass carafes in your warehouse come in the same size box as the filters do, but are heavier. Also, they've been stored farther away from the shipping center of your warehouse because they aren't shipped as often.
Stacking pallets with more than one type of product has shifted from an exception to the general rule. If you receive a pallet full of 1ft. by 1 ft. boxes that are only labelled with a barcode, how do you ensure laborer safety and accurate storage?
Automated storage and retrieval systems (AS/RS) is the answer. An AMR can scan barcodes, apply the correct amount of force to lift whichever box, load a combination of boxes, and then transport them to the correct location.
Using AS/RS has a few benefits:
The robot doesn't assume that a glass carafe box (heavy) is a filter box (light), and thus doesn't injure itself and incur lost time or high costs for rehab.
Multiple AGV's performing AS/RS can "communicate" with each other via WMS to avoid inefficient pathways to and from sorting stations.
A robot transporting heavy products doesn't get tired or accident-prone no matter how far it has to travel.
Sensors and Robots Work Together to Automate Inventory
The efficiency and productivity from making the investment to implement warehouse automation can't be overstated. Combining sensors for inventory awareness and AMR's/AGV's for re-stocking and storing decreases the time humans spend on these menial, repetitive tasks.
Beyond decreasing injuries and accidents, there are other benefits to automating warehouse and manufacturing processes. The less time humans perform manual processes, the more time they have to strategize, innovate, and otherwise improve the customer/client experience.
High-quality sensors are imperative in the use of AMR's and AGV's. Mobile robots depend on LiDAR, radar, sonar, and thermal sensors (among others) to avoid damaging themselves, product, and other robots or humans.
Interested in incorporating sensors in inventory management?
Warehouse Automation Trends & Statistics
Automated Technology Can Decrease Labor Cost and Improve Land Use
Warehouse Automation Technology Is Best for Dealing with Increases in Order Frequency and Complexity
Robots equipped with radar, LiDAR, and other sensors can handle these increases in complexity with efficiency. Whether you need to address changes in pallet assortment or product manufacturing, the automated systems for each are only getting better.
Plus, the warehouse management systems (WMS) that are being developed have improved human-robot interface. This change allows for less specialized training and, therefore, greater employee retention.
Robotics and Autonomous Systems Prevent Customer Dissatisfaction
The changing landscape of products and orders is primarily due to e-commerce. Again, we point to Amazon and other online retailers providing more types of products at faster delivery times.
Previous data states that the number of SKU's in warehouses has been increasing. Add to that the increase in e-commerce prompted by COVID in addition to workforce shortages and you have a great opportunity for warehouse automation.
Your customer satisfaction can improve with autonomous warehouse technology. Combining a WMS built for your industry with high-quality robotics will decrease errors that increase time-to-delivery. What's more, automated systems can help to reduce the burden of speed on employees.
The Time to Invest in Automated Systems is Now
Customers are demanding faster delivery and more accurate inventory management. Are you prepared to rise to the occasion? Failure to adapt could be more expensive than incorporating warehouse automation systems.
AMR's and AGV's may be the answer to this pressing challenge.
Got questions about automation sensors? Please contact our team today! We're a group of dedicated engineers who are eager and prepared to answer your automated systems questions.
Add New Comment