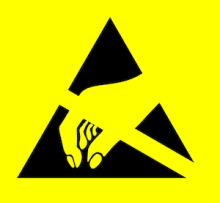
When USB robustness and reliability matter
For everyday use — like connecting a mouse or webcam to your laptop — an inexpensive USB hub with enough ports will get the job done. However, in production or test environments, robustness and reliability are paramount. Chasing bugs inherent in inexpensive USB hubs is distracting and time-consuming, and failed processes can shut down lines or negatively impact your product quality. Even worse, a cheap hub may be able to damage your critical production systems.
If you have experienced this, you know how important a USB hub with robust design, suitable for a production environment, can be. It is therefore very important to consider the true cost and impact of the USB hub to your company as you specify equipment that meets your reliability needs for real-world production testing.
Acroname's S77 USBHub2x4 is designed from the ground up by engineers who understand these issues intimately and have addressed them - to keep your lines running. Acroname evaluated four different "industrial" USB hubs for robustness and reliability in production environments. Specifically, we looked at each design for:
- ESD and surge current protections
- Current limiting
- Inrush current mitigation
In this series of three articles, we will review each design for these critical design considerations for USB hubs intended for production environments. As the first article in the series, we will introduce the contenders and then look at their designs for ESD and surge current robustness.
At first glance, a hub is a hub — but not all hubs are created equal. Of course, there are differences in functional specifications:
- Bus-powered or self-powered
- Number of ports
- Connector types
- USB 2.0 Speed (1Mbps, 12Mbps or 480Mbps) or SuperSpeed (5Gbps or 10Gbps)
However, after choosing the functional specs you need, it is important to consider the design behind the numbers.
Build quality, proper treatment of grounds and shields, current limiting, electro-static discharge (ESD) and surge protection might not make much difference to your mouse, but they are all critical considerations in a production environment. Just because a USB hub comes in a metal housing or is labeled "industrial" doesn't mean it was designed to be rugged or reliable.
USB Hub Electrostatic Discharge (ESD) Comparison
The Contenders
We have disguised the brand names of these four hub suppliers, referring to them with single letters: “X”, “T”, “L” and “S”. Each of these hubs were purchased from reputable online vendors and were advertised for use in industrial environments. All except Hub T claimed to have ESD protection up to ±15kV; Hub T did not specify an ESD rating. The prices for the hubs varied widely, too. The following table shows the range of prices found for the same brand and model of each hub.
Hub X $120-149
Hub T $99-119
Hub S $40-79
Hub L $53-69
First up is Hubs X and T. You're not seeing double. Hubs X and T are exactly the same under their metal covers. Both hubs are branded by European companies, but the hardware is actually made by a Taiwanese ODM. White labeling is common for commodity products like USB hubs. Unfortunately it means that repeat purchases of the same brand and model might result in different hardware since the vendor may switch to other white label hardware any time. If you’re trying to scale out production systems, you need to know you can get the same hardware every time, but this can be difficult when relying on white label vendors. We’ll drop Hub “T” and just look at Hub “X”.
Hub X and T: Same on the inside; different on the outside
From left to right: Hub X, S and L.
Design for ESD and Surge Current Robustness
Hub X
Hub X, in its various incarnations, claims ±15kV ESD protection or just “industrial”. This hub has no external ESD protection, and it uses the ViaLabs VL811 chipset. Data sheets for the VL811 aren’t available. The VL812 claims ESD immunity to ±2kV HBM. The HBM specification uses far lower current than the IEC-61000-4-2 standard, so a 2kV HBM is 90 times lower power than the IEC standard (On Semi TND410/D). Assuming the VL811 is similar, the 2kV HBM ESD specification of the VL812 is likely not useful in production environments, so the chipset should have external ESD and transient voltage suppression added.
Unfortunately, Hub X does not add any extra ESD or transient voltage protection to USB signals, meaning common ESD strikes when cables are connected can affect the sensitive hub controller. The USB connector is designed to make connections in a specific order; shield, ground and power (Vbus) and then data lines. Careful design handling of the shield and ground signals can add a reasonable level of protection against this common strike vector. However, Hub X’s design directly ties USB shield and ground at the USB connectors. As such, any ESD event from connecting a cable would likely be directly injected into the ground plane of the hub controller. Such events could force transient currents of 30-100 amps across the ground plane, through the hub controller IC and into the supply planes and data lines. These events could also raise the ground plane which are connected to the host computer and other devices, causing cascading failures across the bus. Inappropriately handled ESD events like this could cause resets or irreparable damage to the hub or even a connected host computer. Such damage would dramatically raise the ”cost" of this cheap hub.
Hub X does have several ferrite beads (SMT and through-hole) on the external power inputs. Their placement and sizing would make them useful only for noise suppression, not ESD or surge currents. Also, bi-directional transients would completely bypass the ferrite beads through the shield connection to ground.
Hub X has footprints for common-mode chokes on the USB differential data lines, but these were not installed. Usually such common-mode chokes are used for noise suppression and EMI/EMC compliance, but they can also be useful for mitigating some energy from ESD currents. Adding these chokes would be "better than nothing”, but hub X opts for nothing.
The final ESD related design flaw in Hub X: LEDs. Simple indicator LEDs are useful and seem innocuous from an ESD perspective. However, LEDs are notoriously sensitive to ESD, and Hub X has 5 through-hole LEDs pushed through its metal housing. These protrusions are essentially ESD antennas. Many times, an ESD strike to an LED will simply destroy the LED, but in other cases, the currents will travel into the ground planes, power planes, and any drive circuitry. In Hub X’s design, these LEDs are driven by the hub controller without even a current limiting resistor in the series. An ESD strike to one of its LEDs would likely destroy the hub controller.
While evaluating hub X, we had 2 of the 4 downstream ports stop working just from plugging in standard devices. This occurred in normal lab environment, without applying any kind of stress testing. We suspect ESD damage to the hub controller.
Hub X Design Details
Hub S
Turning to Hub S, we see some modest improvements over Hub X. The hub controller is a Terminus Technology's FE1.1s, a common Taiwanese chipset found in low-cost USB hubs. The FE1.1s data sheet specifies a ±2kV ESD rating. This is a bit short of the ±15kV printed on the box and housing, so we would hope to see some additional ESD protection surrounding the hub controller.
Close to the downstream connectors are pairs of passive components connected between the USB data lines and ground. These components have reference designator prefixes of “R”, indicating a resistor of some type, and are a translucent green color. This would lead one to believe these are multi-layer varistors (MLV). See R16, R21, R12 and R13 in the hub S detail picture. In this application, the MLVs start with high resistance and would gradually reduce their resistance as current is driven through them. These components could therefore shunt high voltages on the data lines to ground. However, this use of MLVs relies on internal heating of the component, so they would change resistance on the order of milliseconds to seconds. As such, they would have little effect on an ESD strike, which is measured in nanoseconds. These might provide some protection to over voltage on the data lines, but again, since they cannot respond to nanosecond events, the hub controller would likely be destroyed before any significant MLV response occurred. While we aren’t going to get into USB data signal integrity, it’s worth mentioning that MLVs connected high-speed signal lines is not a good design practice. These components would have widely varying intra-part capacitance which would also vary with temperature. This varying parasitic capacitance would degrade the USB data signal integrity and could lead to intermittent connectivity failures.
While the designers implemented some ESD protection on the data lines, the other signals on the USB connector remain exposed: Vbus, ground and shield. Ground and shield are directly shorted at the connectors on Hub S, bringing all the same risks as those on Hub X. The Vbus line only has a small ceramic capacitor in parallel with a large electrolytic capacitor. While capacitors can help to “smooth out” the energy from an ESD strike, they aren’t effective alone since they cannot quickly dissipate ESD energy except through their equivalent series resistance (ESR). ESD strikes can be thought of as short duration high-frequency signals. Since capacitors tend to act as short circuits at high frequencies, they will tend to conduct ESD energy into the planes they are connected between. In Hub S, ESD strikes to Vbus will cause large voltage spikes on the 5V and ground planes. These spikes could destroy the hub controller, the power supply, and other devices on the bus since ground and shield are connected.
This hub does have foot prints for LEDs on each downstream channel which would have protruded through the metal housing. These placements were not populated. Whether for cost cutting or ESD immunity improvement, it was a wise choice to drop the LEDs.
Hub S’s power inputs also have no true ESD protection. This leaves the wide-range voltage input switch mode power supply vulnerable. To make matters worse, there are several MOSFETs, which have ESD-sensitive gates, placed near the input power connectors. It is likely that hub S would turn off if an ESD strike near the input power connectors. And it would likely never turn on again.
Hub S detail
Hub L
Comparing Hubs X and S to Hub L, it is clear that the design appears to be simplified. Hub L has far more components, and appears to have improved ESD robustness. Close to each connector there is a small bi-directional TVS diode for the USB data signals. These TVS diodes will shunt high voltages to ground or the 5V plane. It is debatably better to shunt the energy to the shield, but Hub L’s inclusion of the TVS diodes is a big step above the other designs.
The other hubs failed to properly treat the ground shield signals separately. Hub L takes an acceptable approach. Ground and shield are capacitively coupled small (100nF) ceramic capacitors near each connector. At one of the connectors, a high resistance (1MΩ) “drain” resistor ties the the ground and shield together. This allows the ground the shield to “float” during short events like ESD strikes, but eventually return to equipotential to prevent ground loop currents in the shield.
On the USB Vbus lines, Hub L inserts a series ferrite bead. These can be effective at mitigating power supply noise and EMI issues, and they can be somewhat beneficial for reducing currents from ESD strikes. Further, on the bottom side Hub L has a large TVS or zener diode. Any ESD energy on the Vbus line would be mostly conducted into the hub’s ground plane. Its arguable whether this energy should be sent to shield instead of ground, but the Hub L design is appropriately protecting the Vbus line from ESD strikes.
This hub has one LED for power indication, and it protrudes through the metal housing. An ESD strike to this LED would likely cause the LED to not light up. Unfortunatley, ithe LED might not light either because it or the power supply was destoryed.
Hub L is the only hub in the roundup that provided protection for the power input. The inputs have rectifying diodes and TVS diodes interconnected between power, return and earth. Any ESD energy on any of the input pins would be shunted to ground and eventually earth. This added substantial cost to the hub, but it is an effective way to protect not just the hub, but all the customer’s equipment that gets connected to it.
Hub L detail
Bonus: Acroname S77 USBHub2x4
Acroname’s USBHub2x4 draws from over 20 years of industry experience designing and supplying robust electronics for challenging environments. Every external signal is protected against ESD and surge currents with high-speed, low-capacitance TVS diodes. Ferrite beads in series with Vbus further suppress ESD currents and mitigate interference. Shield and ground signals are capacitively coupled and are tied with a high value bleed-off resistor. There are no LEDs protruding beyond or sitting near the metal housing. The USB hub controller and embedded microcontroller also include internal ESD protections. When testing the USBHub2x4 device at a certified lab, the device remained functional after being exposed to ±30kV contact-discharge strikes. This thoroughly exceeds the requirements of the IEC-61000-4-2 test standard and pushed the limit of the available test equipment in the lab.
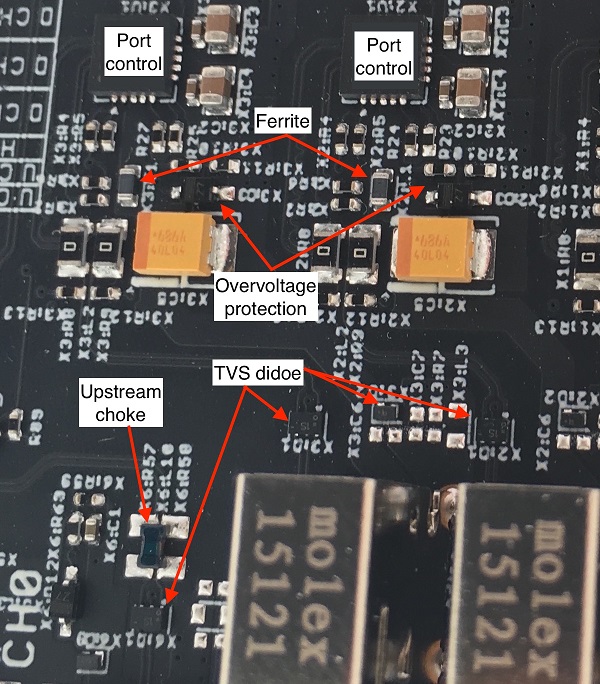
Acroname S77 USBHub2x4 detail
Made with the newest components and design practices to focus on industrial and robustness
When installing any equipment into a production environment, it is important to consider more than the brand, labeling or marketing bullet points. Even a common product like a USB hub can be the downfall of complex and expensive production environments. Trust your equipment to engineers who design for true industrial environments.
Acroname-designed products are architected with the newest components and design practices that focus on industrial and robustness. Even better: our products are tested by certified test houses to conform to or exceed industry standards and compliance specifications. Acroname's products are field tested and purchased by customers who depend on them to work reliably in real-world industrial environments. Real-world industrial reliability by design. Always.
Our next article in this series will analyze these same hubs with focus on downstream USB Vbus current limiting. Stay tuned!
Add New Comment